Direktmotoren oder Direktantriebe sind heute in vielen Bereichen der industriellen Automation eine etablierte Technologie. Auch in Bereichen, die bisher eher traditionellen Systemen vorbehalten waren, findet diese […]
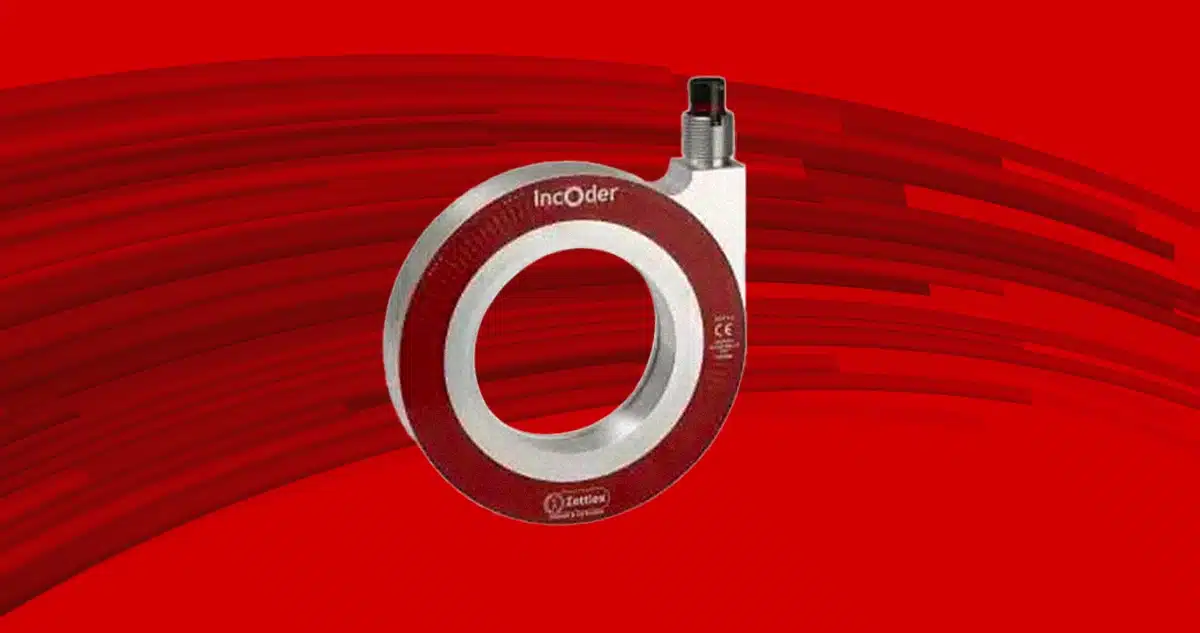
Direktmotoren oder Direktantriebe sind heute in vielen Bereichen der industriellen Automation eine etablierte Technologie. Auch in Bereichen, die bisher eher traditionellen Systemen vorbehalten waren, findet diese Art der Motorisierung zunehmend Anwendung. Dieser Artikel vergleicht mögliche Lösungen und sucht nach ihren Vorteilen und Kritikpunkten.
Terminologie
Theoretisch kann der Begriff Direktmotor oder Direktantrieb auf jeden Motor angewendet werden, auf den die Last direkt und ohne weitere Übertragungselemente wie Zahnräder, Riemenscheiben, Ketten oder Getriebe wirkt. In der Regel handelt es sich um bürstenlose Permanentmagnet-Synchronmotoren, die ihr Drehmoment direkt auf die Last übertragen. Sie werden häufig entlang des Durchmessers entwickelt, enthalten gleichzeitig die Höhe und sind durch eine Durchgangsbohrung gekennzeichnet. Sie werden als Torquemotoren bezeichnet und entwickeln bei allen Drehzahlen bis zur Nenndrehzahl ein konstantes Drehmoment.
Wie funktioniert ein Direktantrieb?
Direktantriebe funktionieren ähnlich wie bürstenlose Motoren. Die Magnete sind mit dem Rotor verbunden, während die Wicklungen auf dem Stator des Motors angeordnet sind. Wenn die Wicklungen erregt werden, erzeugen sie ein Magnetfeld, das die Rotormagnete anzieht oder abstößt und so deren kontrollierte Drehung bewirkt. Es gibt sowohl rotierende als auch lineare Direktantriebe.
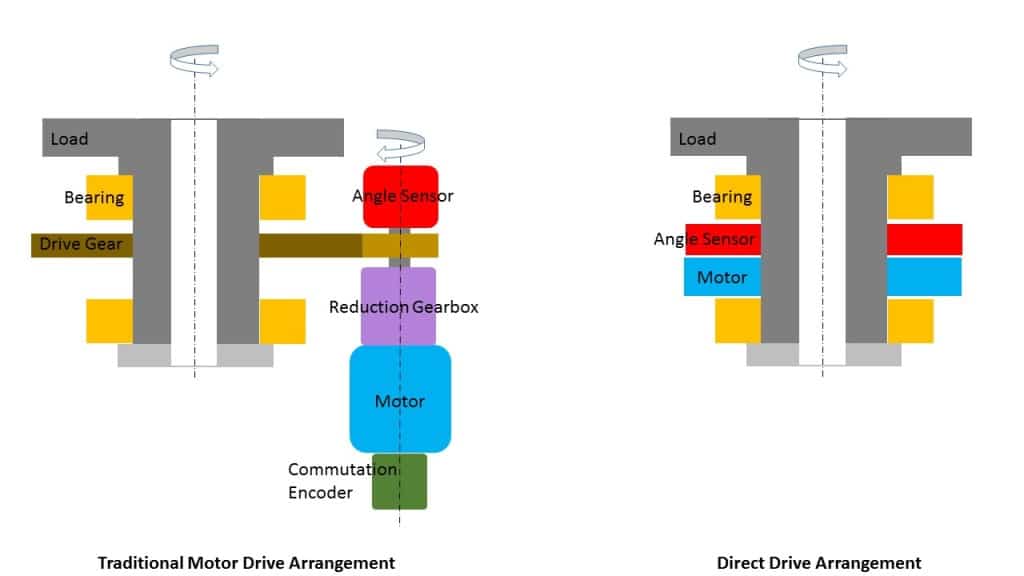
Direktmotoren haben in der Regel viele Pole (>20 und manchmal > 100); es gibt Torquemotoren mit 1 m Durchmesser, die Drehmomente bis zu 10 KNm erzeugen können. Viele werden als rahmenlose Motoren ohne Gehäuse, Lager und Rückführungssensor angeboten. Dies ermöglicht es Maschinenbauern oder Integratoren, das Gehäusedesign zu vereinfachen und die Welle und die Lager so zu dimensionieren, dass ihre Form, Größe, ihr Gewicht und ihre dynamische Leistung optimiert werden.
Das Verhältnis von Drehmoment zu Trägheit ist höher als bei herkömmlichen bürstenlosen Motoren; außerdem haben sie eine niedrige elektrische Konstante. Dies bedeutet, dass das Drehmoment schnell aufgebracht wird, wenn die Spannung eine ausgezeichnete Systemsteifigkeit erreicht. Herkömmliche Motoren sind darauf ausgelegt, ein maximales Drehmoment bei hohen Drehzahlen zu erzeugen, in der Regel über 1000 U/min, und sind auf die Nennleistung ausgelegt. Torquemotoren hingegen werden normalerweise nach dem maximalen und kontinuierlichen Drehmoment und nicht nach der Leistung dimensioniert.
Pro und Kontra
Die wichtigsten Vorteile der Verwendung von Direktmotoren sind:
Hohe dynamische Leistung und Genauigkeit bei der Positions- und Geschwindigkeitsregelung
- Freiheit von Spiel und Verschleiß
- Hohe Zuverlässigkeit: da es keine mechanischen Teile wie Zahnräder, Riemenscheiben, Dichtungen, Lager gibt
- Kompaktheit: Sie entwickeln sich aus dem Durchmesser, haben eine geringere Höhe und ein zentrales Loch
- Andere Drehmoment-Trägheits-Verhältnisse und ein anderes Drehmoment-Masse-Verhältnis des Direktmotors
- Niedriges Rastmoment (cogging)
- Hohes Drehmoment bei niedrigen Drehzahlen
- Hohe Energieeffizienz: durch den Verzicht auf zusätzliche mechanische Elemente
- Geräuscharm und geringe Eigenschwingungen
- Abwesenheit von Wartung
- Geringe Kühlleistung: durch die besonders günstige mechanische Geometrie
- Relativ großer Luftspalt: mit guter Schlagfestigkeit und ausgezeichneter Lösung in staubiger Umgebung
Die Gründe für einen Konstrukteur, sich für einen Direktmotor zu entscheiden, sind die mögliche erreichbare Leistung und die größere Dynamik als bei herkömmlichen Lösungen. Vor allem ist die Durchgangsbohrung eine Lösung für die Durchführung von elektrischen Verteilern, Pneumatikschläuchen und elektrischen Kabeln.
Der größte Nachteil ist oft eher ein gefühlter als ein tatsächlicher: Direktantriebe sind manchmal teurer als herkömmliche Motoren. Dies ist häufig der Fall, wenn man die Kosten der Antriebe vergleicht. Bei einer sorgfältigeren und umfassenderen Bewertung, bei der die wegfallenden mechanischen Teile, die allgemeine mechanische Vereinfachung und der geringere Wartungsaufwand berücksichtigt werden, sind Direktantriebe jedoch auch in wirtschaftlicher Hinsicht eine gute Lösung. Hinzu kommt, dass die Kosten für Direktmotoren allmählich sinken, was zum Teil auf die Verfügbarkeit leistungsfähigerer Neodym-Eisen-Bor-Magnete (Nd-Fe-B) und die exponentielle Zunahme der Verwendung dieser Antriebe zurückzuführen ist. Ein typisches Beispiel sind sehr kostensensible Anwendungen wie Waschmaschinen, wo herkömmliche Motoren durch Torque-Motoren ersetzt werden, die Riemen und Riemenscheiben überflüssig machen und die Bewegungsübertragung leiser und zuverlässiger machen. Wichtige Anwendungen von Direktantrieben finden sich in CNC-Werkzeugmaschinen, Verpackungsanlagen, Robotik, Radarsystemen, Militär, Telekommunikation, Drehtischen und Teleskopen. Die Palette wächst, und für die nahe Zukunft wird eine weitere Expansion erwartet.
Die meisten konventionellen Motoren weisen von Natur aus ein starkes Drehmoment-Cogging auf, aber angesichts der hohen Betriebsgeschwindigkeit ist dieser Effekt für die endgültige Leistung oft unbedeutend. Direktantriebe leiden unter Umständen stärker unter diesem Nachteil, es sei denn, es wird eine Rückkopplung mit höherer Auflösung eingesetzt. Dies ist sicherlich ein Punkt, der den Einsatz dieser neuen Antriebe verlangsamt hat, da sie mit anspruchsvolleren Steuerungen gesteuert werden.
Aber auch im Bereich der Steuerungen wurden beachtliche Leistungen erbracht, die zu erschwinglichen Kosten zu Abtastzeiten von mehr als 4 KHz führen.
Einer der größten Vorteile von Torquemotoren ist die direkte Übertragung und die höhere Genauigkeit bei Positionierung, Drehzahlregelung und Dynamik. Anstatt die Last mit einer Kupplung, Ketten oder Riemen zu verbinden, führen Zahnräder oder Riemenscheiben die Motorflansche direkt zur Last; es gibt keine Hysterese, kein Spiel und keinen Bewegungsverlust, unabhängig von der Richtung der Positionierung. Diese Vorteile sind jedoch nur mit einem hochauflösenden Rückmeldegerät möglich. Hallsensoren, die üblicherweise für Leistungsschaltungen verwendet werden, bieten nicht die geeignete Leistung, um eine genaue Positionierung und eine angemessene Drehzahlregelung zu ermöglichen.
Wenn die direkte Motorbohrung klein genug ist, d.h. weniger als 50 mm, gibt es eine breite Palette von Rückmeldungen, die auf optischer, magnetischer oder induktiver Technologie basieren. Da die meisten Positionssensoren eine Bauform haben, die eine kleine Eingangswelle aufweist, hat dies zu einem Problem bei der Integration von Torquemotoren geführt.
Die erste Möglichkeit ist der Einsatz eines optischen Drehgebers mit Gleichstromversorgung und absolutem oder inkrementellem Digitalausgang. Sie sind nicht für staubige oder flüssige Umgebungen geeignet, da dies die korrekte Signalerzeugung beeinträchtigen würde. Außerdem schränken die sehr engen Toleranzen, der enge Temperaturbereich und die starke Empfindlichkeit gegenüber Stößen ihre Verwendung ein. Mit kapazitiven Drehgebern können diese Probleme überwunden werden, aber die mögliche elektrostatische Entladung ist begrenzt. Magnetische Encoder haben aufgrund der magnetischen Hysterese eine geringe Genauigkeit und sind außerdem sehr empfindlich gegenüber den vom Motor erzeugten Magnetfeldern. Die traditionellste Lösung sind Resolver, die eine hohe Zuverlässigkeit und Anwendungssicherheit bieten, insbesondere in der Luft- und Raumfahrt und im Verteidigungsbereich. Sie sind jedoch sehr sperrig, schwer und teuer, insbesondere bei Bohrungen über 50 mm.
Ein neuer Ansatz
Ein neuer Typ von Positionssensoren wird zunehmend als Rückmeldung für Torque-Motoren eingesetzt, egal ob induktiv oder incOders. Sie arbeiten nach dem gleichen elektromagnetischen oder induktiven Prinzip wie Resolver, verwenden aber anstelle von sperrigen Transformatorwicklungen laminierte Leiterplatten und sind damit preiswerter, kompakter und leichter. Anstelle der komplexen AC-Stromversorgung und der Signalverarbeitungsschaltungen, die bei Resolvern erforderlich sind, verwenden IncOder einfache elektrische Schnittstellen, ähnlich denen, die bei optischen Encodern verwendet werden, sowie eine DC-Stromversorgung und einen digitalen Ausgang.
IncOder sind in absoluten oder inkrementalen Formaten, A- und B-Signalen, mit Auflösungen bis zu 22 Bit, etwa 4 Millionen Zählungen pro Umdrehung, erhältlich. Die Genauigkeit beträgt weniger als 40 Bogensekunden oder 0,01° und der Wärmeausdehnungskoeffizient ist mit weniger als 0,5 ppm/K sehr niedrig. Die dynamische Leistung wurde durch Erreichen von Aktualisierungsraten von 10 KHz verbessert. Auch konstruktiv sind sie ideal für Anwendungen mit großem Durchmesser, sehr niedrigem Profil und großer Durchgangsbohrung. Sie können ohne zusätzliche mechanische Teile wie Lager, Dichtungen oder Kupplungen mechanisch mit dem Direktmotor verbunden werden.
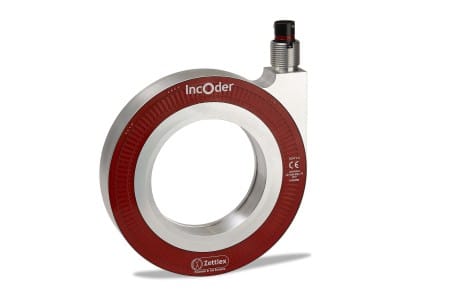
Die Kombination von IncOders und Torquemotoren wird von vielen Integratoren zunehmend bevorzugt. Die Ergebnisse bestätigen, dass sie eine hochzuverlässige, dynamische und präzise Positionierungssteuerung auch für medizinische, luft- und raumfahrttechnische, industrielle und petrochemische Systeme ermöglichen.