Schrittmotoren (oder Steppermotoren) werden in einer Vielzahl von industriellen Anwendungen eingesetzt. Sie sind preiswert, einfach zu bedienen und bieten ein hohes Drehmoment bei niedrigen Drehzahlen. Dieser […]
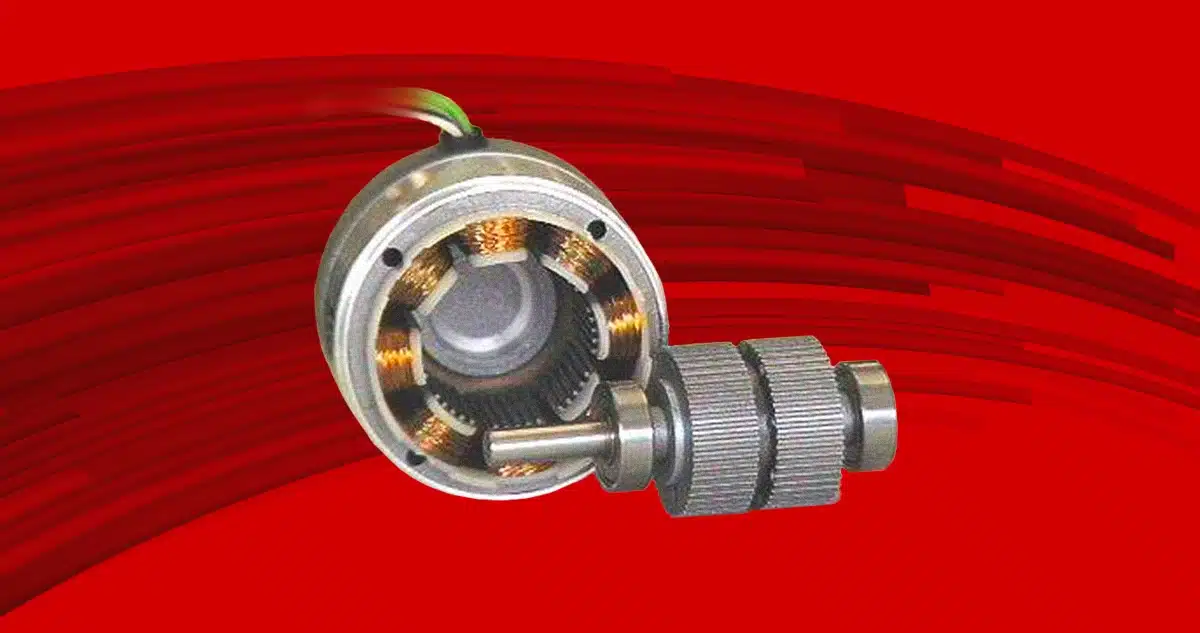
Schrittmotoren (oder Steppermotoren) werden in einer Vielzahl von industriellen Anwendungen eingesetzt. Sie sind preiswert, einfach zu bedienen und bieten ein hohes Drehmoment bei niedrigen Drehzahlen. Dieser Motortyp hat jedoch einige Nachteile, die in der Entwurfsphase berücksichtigt werden müssen: Sie können die Steigung verlieren, wenn das erforderliche Drehmoment größer ist als das verfügbare Drehmoment, das Drehmoment fällt mit zunehmender Geschwindigkeit drastisch ab, sie haben hohe Resonanzfrequenzen und einen hohen Stromverbrauch, selbst wenn nur der Motor stillsteht. Galil verfügt über drei geregelte Antriebsmethoden, um diese Nachteile zu minimieren – Korrektur am Endpunkt der Positionierung, Mikroschrittregelung im geschlossenen Regelkreis und Motorantrieb wie ein bürstenloser 2-Phasen-Motor.
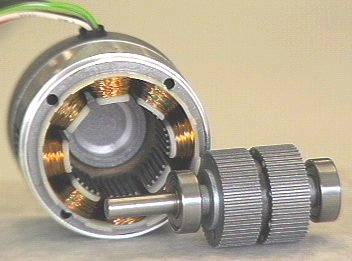
Quelle: http://www.vincenzov.net/tutorial/passopasso/stepper.htm
Die Grundlagen eines Schrittmotors
Der Stator ist ein Satz von Wicklungen, und der magnetische Kreis besteht aus 4 oder, häufiger, 8 “polaren Erweiterungen” (acht in dem abgebildeten Foto). Im Inneren des Stators befinden sich kleine Zähne, die denen des Rotors gegenüberliegen. Die Wicklungen erzeugen ein Magnetfeld, wenn Strom durch sie fließt. Von außen kommen die Leistungsdrähte der verschiedenen Statorwicklungen; die Phasen können nach zwei Mustern gewickelt sein: Bei bipolaren Motoren gibt es nur 2 Wicklungen, und es kommen 2 Drahtpaare heraus; bei unipolaren Motoren gibt es 4 Wicklungen, die paarweise antiparallel auf die polaren Ausdehnungen gewickelt sind.
Der Rotor erscheint als ein Paar massiver, gegenseitig identischer, nebeneinanderliegender Zahnräder, die mit der aus einem Magnetkern bestehenden Welle fest verbunden sind; die beiden Räder sind magnetisiert, das eine als NORD, das andere als SÜD; die “Zähne” der Räder bestehen aus ferromagnetischem Material. Die Anzahl der Zähne ist variabel, 50 sind am häufigsten. Die Phasenverschiebung zwischen den beiden Rädern entspricht der Hälfte der Zahnteilung: Der Zahn des einen Abschnitts entspricht also dem Tal des anderen. Um die Welle zu drehen, werden die Wicklungen in einer bestimmten Reihenfolge erregt. Abbildung 2 zeigt eine vereinfachte Darstellung dieses Vorgangs in einem Zweiphasenmotor. Jede Sequenz entspricht der Drehung einer Stufe des Rotors. Typischerweise gibt es 200 Schritte pro Umdrehung. Von der Steuerung gehen 2 Signale aus, das eine, Step genannt, ist ein Rechtecksignal zu jedem Impuls, der einer Verschiebung von einem physikalischen Schritt des Motors entspricht; das zweite Signal ist die Richtung, die durch den High/Low-Zustand des Signals festgelegt wird.
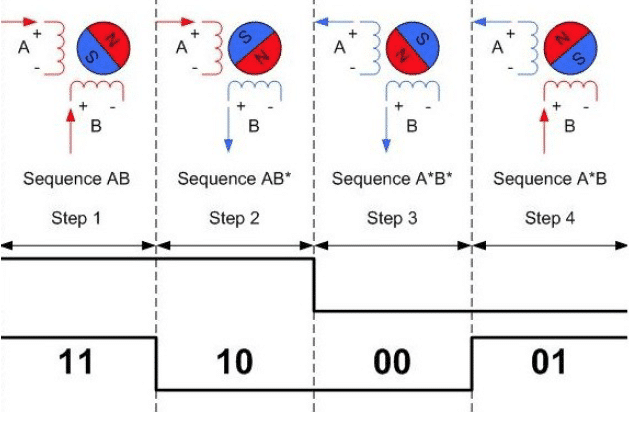
Schrittmotoren sind nicht vor Defekten gefeit. Erstens arbeitet der Motor unter allen Bedingungen mit maximalem Strom, was zu Energieverschwendung und erhöhter Betriebstemperatur führt. Der zweite Fehler ist die Einführung von Vibrationen, die entstehen, wenn sich der Rotor von einem Schritt zum nächsten bewegt. Wenn die Frequenz des Wechsels zwischen aufeinanderfolgenden Schritten der Resonanzfrequenz des Motors entspricht, nimmt die Amplitude der Vibration zu, was zu Positionsverlusten führt. Eine gemeinsame Bedingung für alle Motoren ist der drastische Rückgang des Drehmoments bei steigender Drehzahl. Wenn diese Eigenschaft bei der Konstruktion nicht berücksichtigt wird, kommt es häufig zu Fehlern bei der Motorauswahl. Ein letzter Nachteil von Schrittmotoren ist die geringe Auflösung, die sich aus der Anzahl der Schritte pro Umdrehung ergibt. Wenn eine höhere Auflösung erforderlich ist, kann die Mikroschritttechnologie eine praktikable Lösung sein.
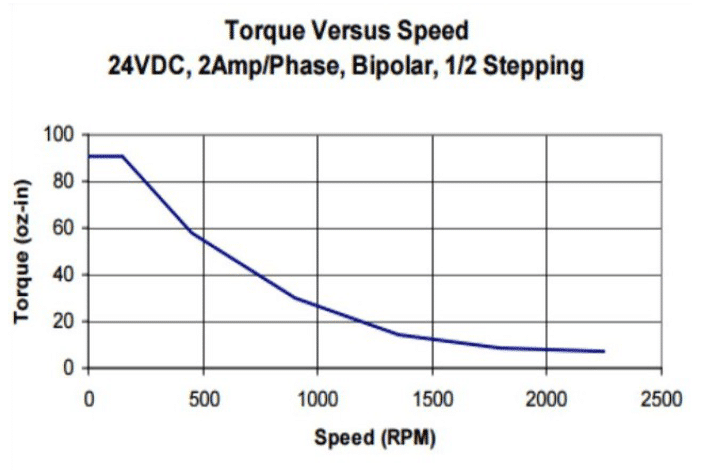
Mikroschrittbetrieb
Microstepping ist eine Methode zur Unterteilung des gesamten Schrittes in kleinere Schritte. Ausgehend von einem Mikroschritt von 2 kann man bis zu 256 Mikroschritte pro ganzem Schritt gehen, was bedeutet, dass ein 200-Schritt-Schritt-Motor eine Auflösung von bis zu 51200 Mikroschritten pro Umdrehung haben kann. Abbildung 4 zeigt das Detail der Stromwellenform für einen einzelnen Schritt durch Erhöhung der Anzahl der Mikrointerpolationen.
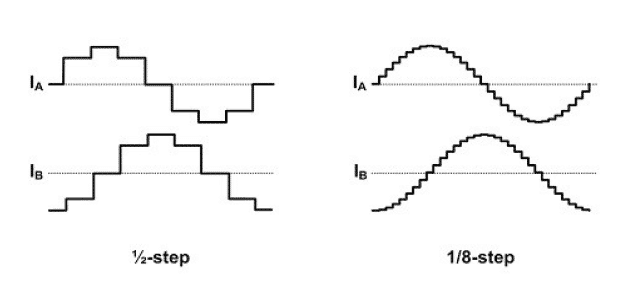
Die mit dieser Regelungstechnik erreichbare Genauigkeit hängt stark von der aufgebrachten externen Kraft ab. Die erreichbare Genauigkeit liegt bei einem ganzen Schritt; ein Motorstillstand wäre die Folge, wenn der Positionsfehler größer als ein halber ganzer Schritt ist. Ein Positionsfehler tritt auf, wenn Reibung, Schwerkraft oder eine andere Kraft groß genug ist, um eine Bewegung zwischen zwei Mikroschritten zu verhindern. Abbildung 5 zeigt die Punkt-zu-Punkt-Positionierung in einem System, das von einem Schrittmotor mit einem Encoder angetrieben wird. Die rote Linie ist die theoretische Position, die violette Linie stellt die Steuerung des Motors dar, und die blaue Linie ist die vom Encoder gemessene Position. Die schwarze Linie zeigt an, wann die Steuerung das Bewegungsprofil aktiviert. Aufgrund von Reibung stimmt die Endposition des Motors nicht mit der befohlenen Position überein, was zu einem stationären Fehler führt.
>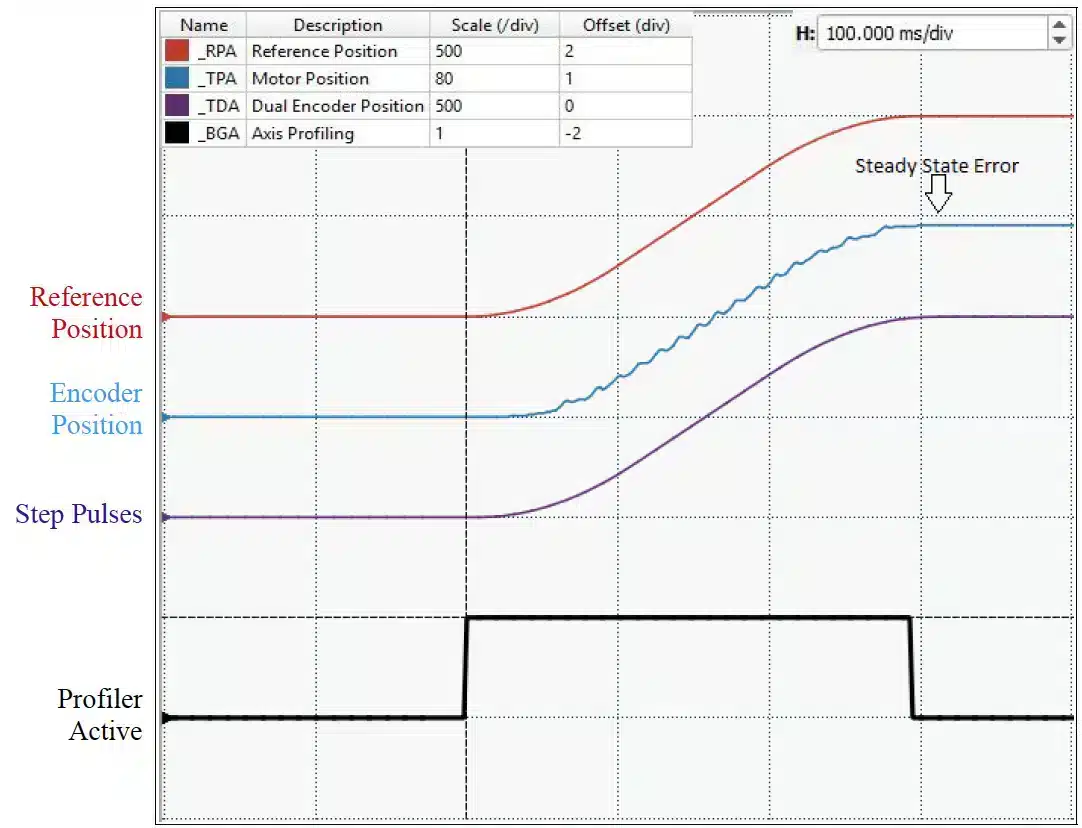
Korrektur am Endpunkt
Durch den Einsatz eines Encoders als Rückmeldung ist es möglich, diese Situation des Positionsfehlers zu erkennen; die Endposition kann durch einen zusätzlichen Befehl so korrigiert werden, dass die Ist-Position der Soll-Position angeglichen wird. Galil nennt diese Art der Ansteuerung Stepper Position Maintenance oder SPM. Der Motor wird immer im Mikroschrittbetrieb gefahren, aber die Genauigkeit des Endpunkts kann überprüft und angepasst werden. Man vergleicht die befohlene Position mit der tatsächlichen Position, bevor die Positionierung beendet wird. Abbildung 6 zeigt das gleiche System wie in Abbildung 5, jedoch mit SPM-Steuerung. Am Ende der Bewegung wird der Positionsfehler erkannt, und ein Korrekturbefehl wird gesendet, um den Motor in die gewünschte Position zu bringen.
>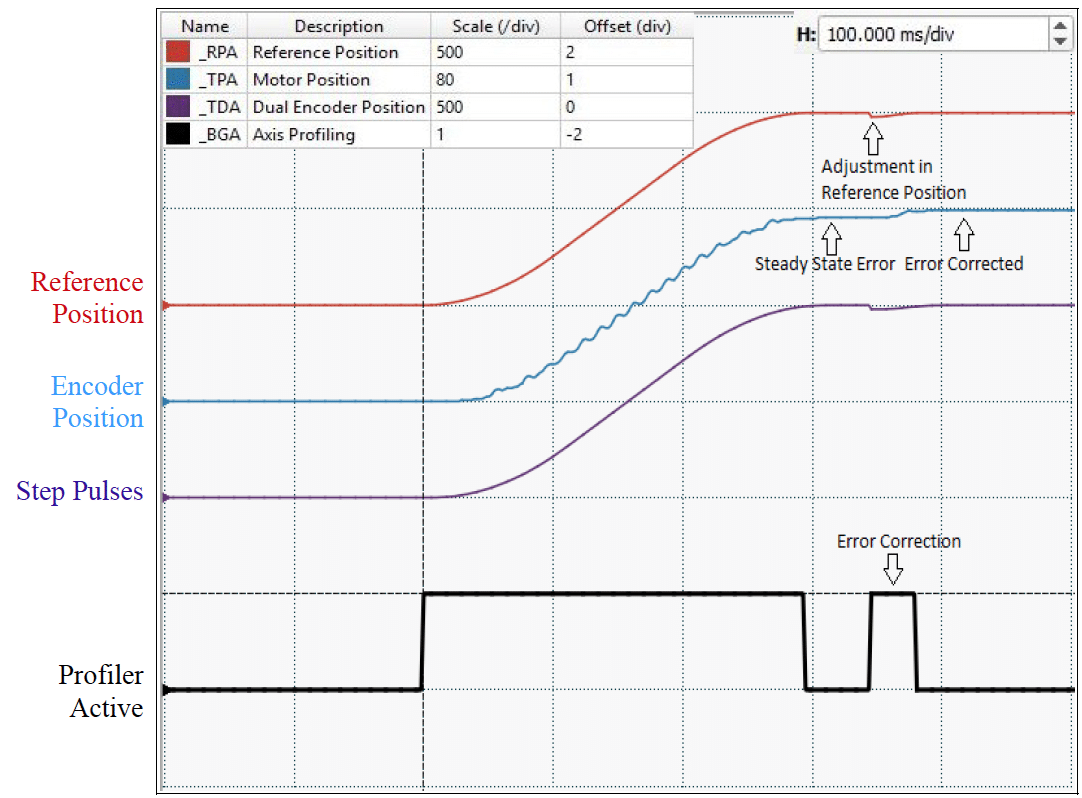
Durch das Hinzufügen des Encoders kann die Steuerung den im System vorhandenen Fehler erkennen und korrigieren. Die Bewegung, die bisher aufgrund der vorhandenen Reibung zu einem stabilen Positionsfehlerzustand führte, kann nun korrigiert werden.
Mikroschritt-Pilot mit geschlossenem Regelkreis
Die Steuerung über den Stepper-Positionserhaltungsmodus ist ideal für Systeme, die nur eine Positionsgenauigkeit am Endpunkt erfordern. Galil empfiehlt die Verwendung von Closed Loop Microstepping oder CLS, wenn eine kontinuierliche Positionsfehlerkorrektur erforderlich ist. Abbildung 7 zeigt die Positionierung im CLS-Modus. Zusätzlich zur befohlenen Position und der tatsächlichen Encoderposition wird intern ein Positionsfehlersignal für die Steuerung (grüne Linie) erzeugt und zur kontinuierlichen Überprüfung der befohlenen Position verwendet. Es ist zu beachten, dass im CLS-Modus der Geber die Position überwacht, die Steuerung aber den Motorbefehl generiert.
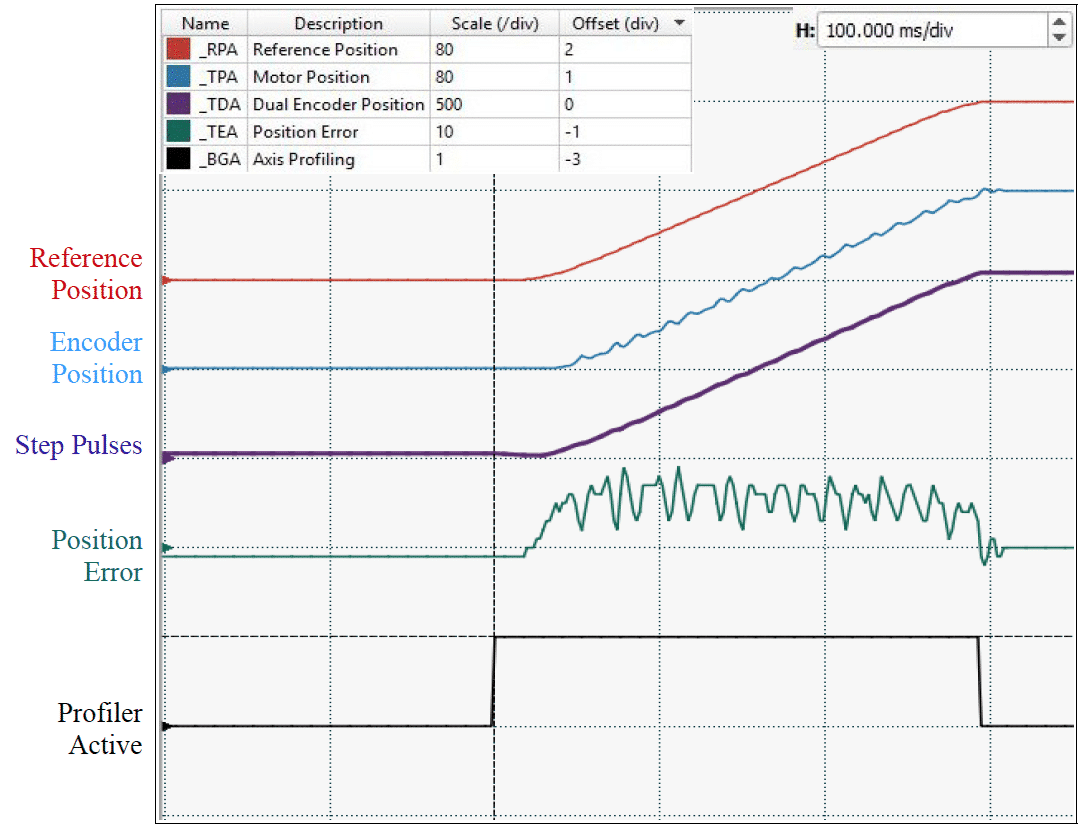
Das Fehlersignal wird von Galils internem Filter analysiert, der jeden Positionsfehler durch Modulation der Steuerschritte zum Antrieb kompensiert. Closed Loop Microstepping ist ein echtes Closed-Loop-System und ist eine “ausgezeichnete Lösung, um einen Schrittmotor traditionell zu steuern. Ein geschlossener Positionsregelkreis birgt das Risiko von Instabilitäten, wenn die internen Filterverstärkungen nicht richtig kalibriert sind. Es bleibt jedoch die Tatsache, dass es sich um ein energieineffizientes System handelt, das im Vergleich zu einem klassischen Servomotor-System eine geringe Bandbreite aufweist. Es sollte bedacht werden, dass die Bandbreite weiter gesenkt werden kann, wenn Treiber von Drittanbietern mit nichtlinearen Eigenschaften eingesetzt werden.
Schrittmotorantrieb als zweiphasiger bürstenloser Motor
Der Schrittmotor kann als zweiphasiger bürstenloser Servomotor angesteuert werden, um maximale Leistung zu erreichen. Der Strom zum Motor wird wie bei einem Servomotor entsprechend der Positionsabweichung geregelt. Das Steuerungssystem, das Galil verwendet, wird als 2-Phasen-Bürstenlos-Modus oder 2PB bezeichnet. Abbildung 8 zeigt das Detail eines auf diese Weise gesteuerten Schrittmotors. Anstelle von Schritten wird von der Steuerung ein analoger Befehl im Drehmomentmodus (braune Linie) erzeugt und an einen der Antriebe gesendet, die in die Steuerung integriert werden können.
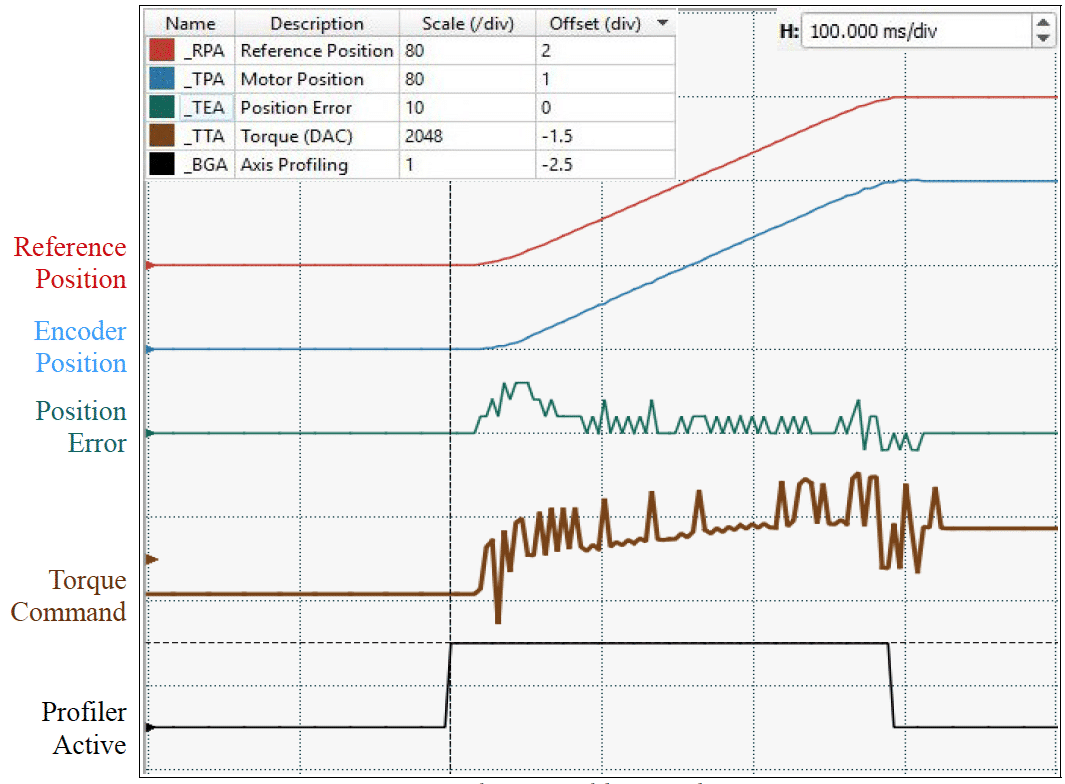
Die Ansteuerung eines Schrittmotors erhöht die Bandbreite durch die Verkürzung der Positionierzeit. Der Motor wird analog zu einem Servomotor mit Getriebe. Da er sich wie ein Servomotor verhält, kann die gesamte Bandbreite des Galil-Filters genutzt werden, einschließlich Notch-, Pol- und Feedforward-Filterung. Um maximale Leistung zu erzielen, muss der Antrieb anspruchsvoller sein, um den für den Antrieb erforderlichen Strom sofort zu erzeugen. In energetischer Hinsicht wird ein höherer Wirkungsgrad erreicht, und der Motor erzeugt weniger Wärme.